Steely Green
Steel production, which is a major contributor to global carbon emissions, has been facing challenges with respect to decarbonisation, but the shift to green methods like ‘DRI-EAF’ is gaining momentum with the rise of carbon pricing and decline of hydrogen costs
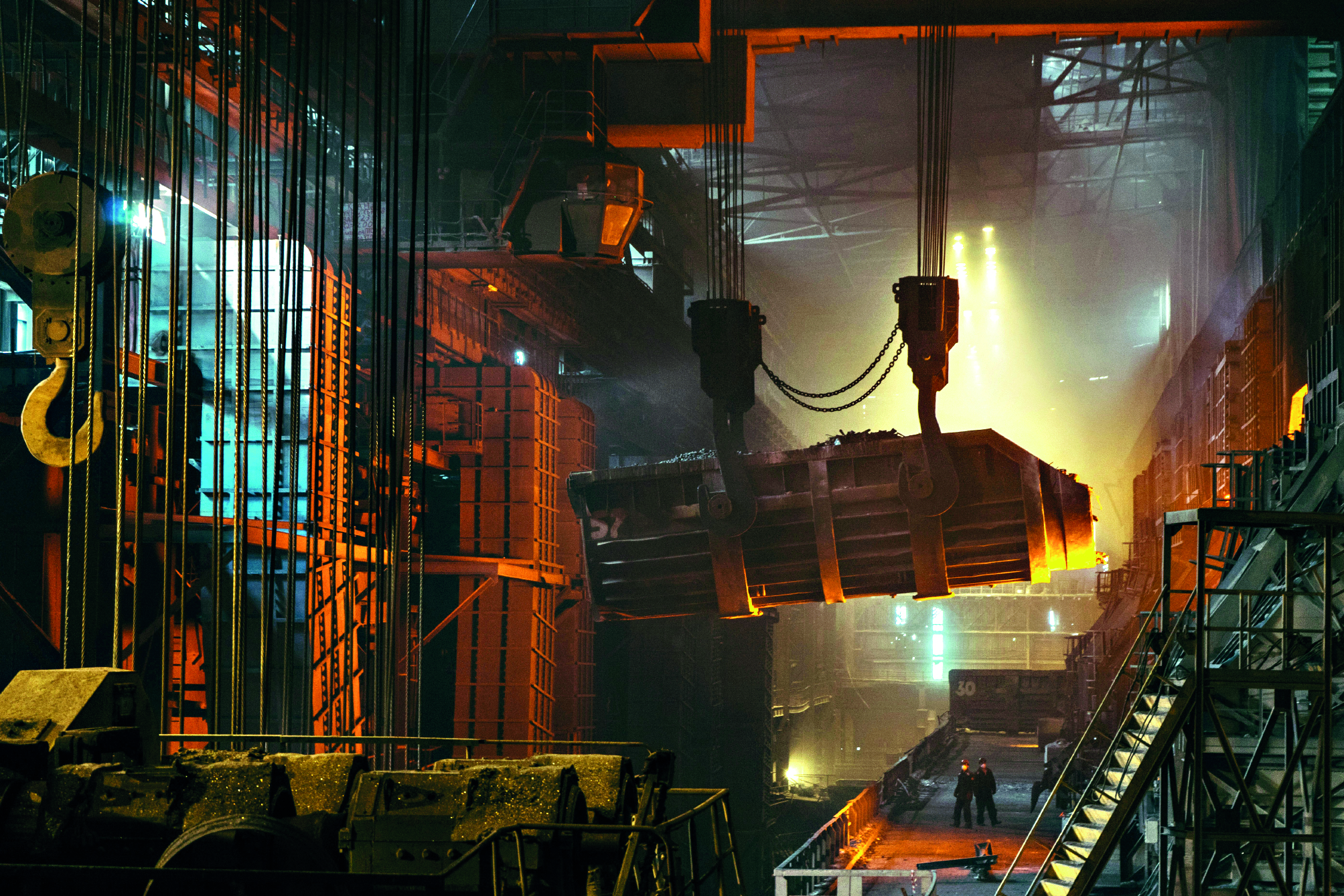
As discussed in the last article, steel is one of the ‘hard to abate’ sectors because of the difficulty in reducing greenhouse gas emissions from steel production. The other such sectors are cement, fertilisers and plastics. In this article, we will discuss the various aspects of conventional steel production and why it is difficult to reduce emissions, the new and ‘green’ production processes and the extent to which they are being adopted across the world.
Why is Steel a ‘Hard to Abate’ Sector?
In the early days of the industrial revolution, steel was produced by the ‘Bessemer’ process, wherein molten pig iron is poured into a large vessel, which is then blasted with air. This oxidizes the impurities such as silica, manganese and carbon, which are separated as slag, leaving behind pure molten iron. This is poured out to make finished steel. The Bessemer process was an inexpensive way of making basic steel. The other way to make steel is through the use of blast furnaces, where coal is first heated to 1000 degrees Celsius to convert it into carbon rich coke. This coke is then used as a reducing agent in a furnace, which is heated to 1500 degrees Celsius, wherein iron ore, which is an iron oxide, is reduced to liquid iron. The oxide reacts with carbon to emit carbon dioxide, leaving behind melted iron, which is again blasted with air to remove other impurities, leaving behind steel. An improvement over the traditional coal burning is the replacement of coal with natural gas to heat the furnace. Both coal- and natural gas-fired blast furnaces emit large amounts of carbon dioxide.
The other way to produce steel is the electric arc furnace (EAF), where heat is produced through the use of an electric arc, which is formed when graphite electrodes react with the iron ore. An electric arc can lead to temperatures as high as 3000 degrees Celsius, with the liquid metal being as high as 1800 degrees Celsius. This is a more environmentally friendly way of producing steel and is being increasingly adopted in the EU.
The most environmentally friendly method of steel production is the DRI Hydrogen Reduction method. This method uses hydrogen instead of carbon for the reduction of iron ore and leads to direct reduced iron (DRI). This is then processed in an EAF described above.
It is important to shift to ‘green’ steel because steel production alone accounts for 11 per cent of carbon dioxide emissions. Even though the cost of production of steel through the blast furnace method is lower than the DRI Hydrogen reduction method, this is likely to change in the future, if countries begin to start pricing carbon. In fact, green steel can become competitive as the price of carbon rises and that of hydrogen falls. With a zero price of carbon, the DRI and EAF method cost of making steel is certainly higher than the blast furnace method. Only with sufficiently cheap hydrogen prices is the DRI-EAF process able to compete with the blast furnace method. However, the situation changes dramatically if the carbon dioxide rises and the hydrogen price drops: in such a scenario, the DRI-EAF method is a clear winner. For example, if the carbon dioxide price rises to USD 15/tonne and hydrogen price is USD 1.5/kg, the cost of steel produced by the DRI-EAF method is lower than that produced by the blast furnace method.
The total crude steel production in the world in 2023 was a little less than 2 billion tonnes. Out of this, China alone accounted for about 50 per cent of the production. India with an output of 140 million tons and the EU with 135 million tons were far behind. The top five steel producing countries in the world are China, EU, India, Japan, USA and Russia in that order. The other large steel producers are South Korea, Brazil and Turkey. Some of the large steel producing companies are the China Baowu Group (China), Arcelor Mittal (EU), Nippon Steel (Japan), Ansteel Group (China) and POCSO Holdings (Korea). Of the total steel production, only 30 per cent was produced by the DRI-EAF method in the world. This figure for the EU was 55 per cent, the US was 63 per cent and India was 56 per cent. The largest producer continued to use the blast furnace method, with 90 per cent of steel coming from it.
Conclusion
Since steel production involves large greenhouse gas emissions and consumption of energy, it is important that the world shift to the DRI-EAF method as soon as possible. With carbon prices rising and hydrogen prices falling, this is happening, but the process needs to be speeded up.
The writer is Additional Chief Secretary, Department of Cooperation, Government of West Bengal