Cementing Sustainability
Cement manufacturing - a major source of CO2 emissions - is facing challenges in adopting greener options, but innovative alternatives in raw materials, kilns, and carbon capture processes can offer promising solutions for sustainable production
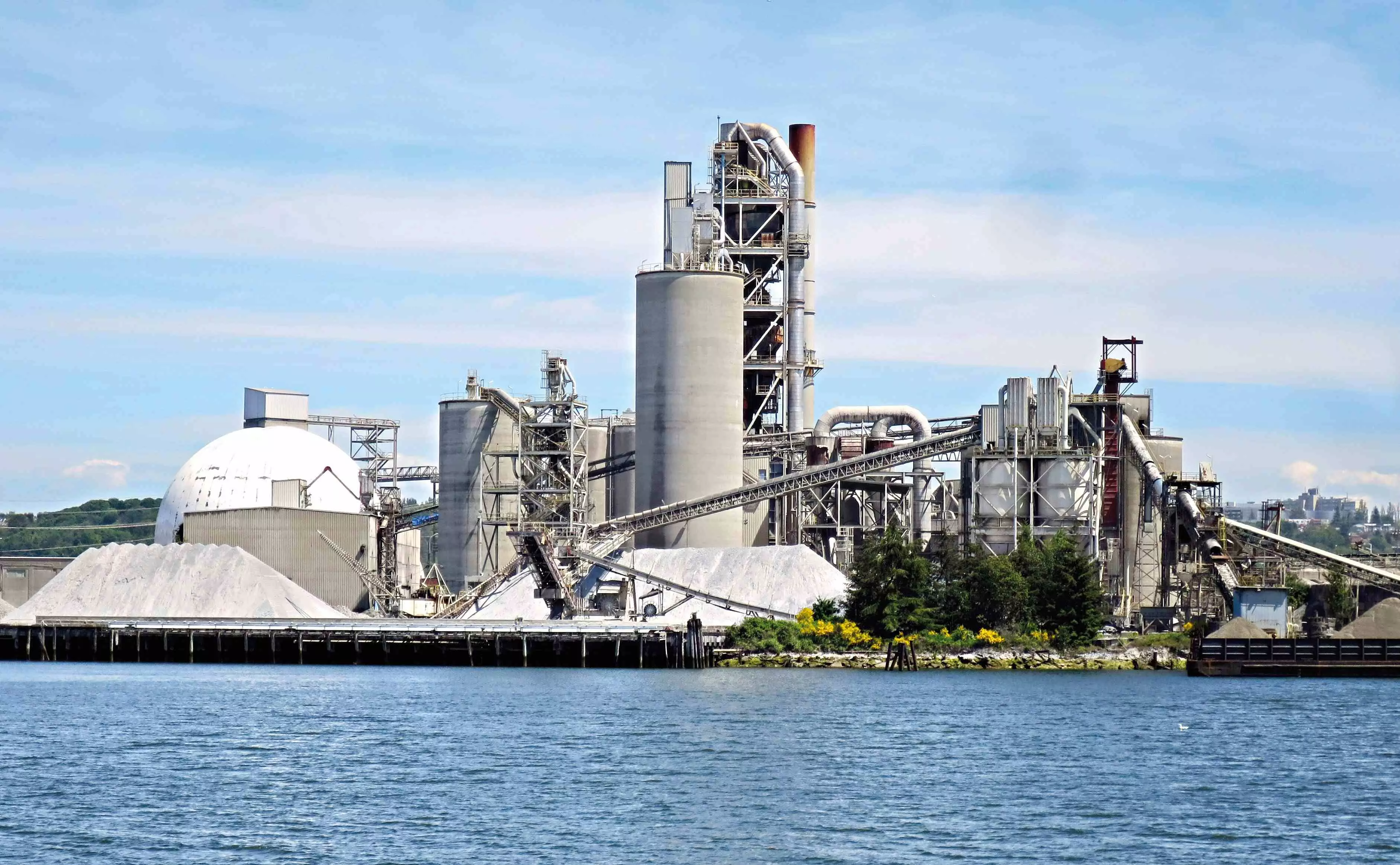
Cement manufacturing is another ‘hard to abate’ sector and responsible for 8 per cent of carbon dioxide emissions worldwide. Furthermore, alternative and better manufacturing methods, which are ‘greener’, have been difficult to pin down. Let us discuss this in more detail here.
Cement Production: A Miracle
Cementing materials, in some form or the other, have been used for thousands of years. Evidence of this has been found in Turkey from excavations dated 12,000 years ago. Later, the Phoenicians, about 3,000 years ago, used burnt lime and volcanic ash (called Pozzolana) to form hydraulic lime, which can harden under water as well. Romans were also experts in using concrete in many of their monuments such as the Pantheon and the Colosseum in Rome.
Cement, as we know today, was first invented by Joseph Aspdin in 1824 by heating limestone and clay, until it was reduced or oxidised. This mixture was then ground and mixed with water. This was called Portland cement by Aspdin, named after the strong building stone found in the Isle of Portland in the UK. In 1845, Isaac Johnson heated chalk and clay at far high temperatures than Aspdin, going up to 1,500 degrees Celsius, which led to clinkering of the mixture and producing cement. While cement is a critical component in infrastructure building, it also emits large amounts of greenhouse gases. When the mixture of limestone and clay is heated at high temperatures in a kiln, the calcium carbonate breaks up into Calcium Oxide and Carbon Dioxide. The clinker that comes out of the kiln is cooled and mixed with gypsum and milled into a powder form. This is nothing but cement. Cement production not only emits carbon dioxide, but is also a very energy-intensive process. According to Paul Hawken’s Drawdown, one ton of cement requires 180 kgs of coal and emits one ton of carbon dioxide. With 5 billion tons of cement production in the world (with half of it coming from China), this translates to 5 billion tons of carbon dioxide annually. A lot of research is going on to make the cement kilns more energy-efficient as well as replace the conventional clinker (that is a major carbon emitter) with alternatives such as volcanic ash, biomass, fly ash and slag, which are industrial waste. This is because the kiln uses 90 per cent of the energy used in cement manufacturing. This has two advantages: the process of making clinker is made more efficient and the fly ash (which would have to be disposed of in a landfill) is used more productively. Other innovations to make cement more ‘green’ are: the incorporation of fibres and special aggregates to make roof tiles and countertops, and treating concrete with chemicals that enables it to absorb carbon dioxide.
Another way to reduce carbon emissions in cement manufacturing is to set up CCUS (Carbon Capture, Utilisation and Storage) plants along with cement plants. While this involves initial capital cost, it will become sustainable as the carbon price rises. A McKinsey study has estimated that cement production will become costlier by 45 per cent by 2050, if a CCUS plant is added, but this will become sustainable as all cement worldwide slowly shifts to capturing carbon. Some of the alternative or ‘green’ cements in the market include Ekkomaxx cement being produced in the US with 95 per cent fly ash and 5 per cent liquid additives. This cement has been approved by the US Green Building Council. Other similar cements include Magnesium Oxychloride Cement (MOC) and Geopolymer cement. While MOC was invented by Sorel in 1867, it has become popular in recent times because of its advantages over Portland cement, such as higher strength, faster setting speed and better thermal insulation. It also emits less carbon dioxide. Geopolymer cement is made by mixing aluminosilicate materials like fly ash with alkaline solutions and has the same advantages as MOC.
Conclusion
Addressing greenhouse gas emissions in cement manufacturing is important because it accounts for 8 per cent of carbon dioxide and 5-6 per cent of greenhouse gas emissions in the world. A number of innovations focused on making the kiln more efficient are being tried out. In addition, the setting up of CCUS plants alongside cement plants is also being contemplated. As these measures take root and spread across the world, emissions from cement manufacturing will fall substantially.
The writer is Additional Chief Secretary, Department of Cooperation, Government of West Bengal